J-STORIES ー 大量に捨てられている生魚の皮を加工し、色とりどりのカバンや財布などの皮革製品として再生する「フィッシュレザー」技術の利用が広がっている。加工した魚の皮は動物皮革に比べても強度が劣らず、魚ごとに異なるうろこの形状が「オンリーワン」のデザインとなるなどファッション性も高い。何より、フィッシュレザーには「自然の恵みを無駄にしない持続可能なものづくり」という価値がある。
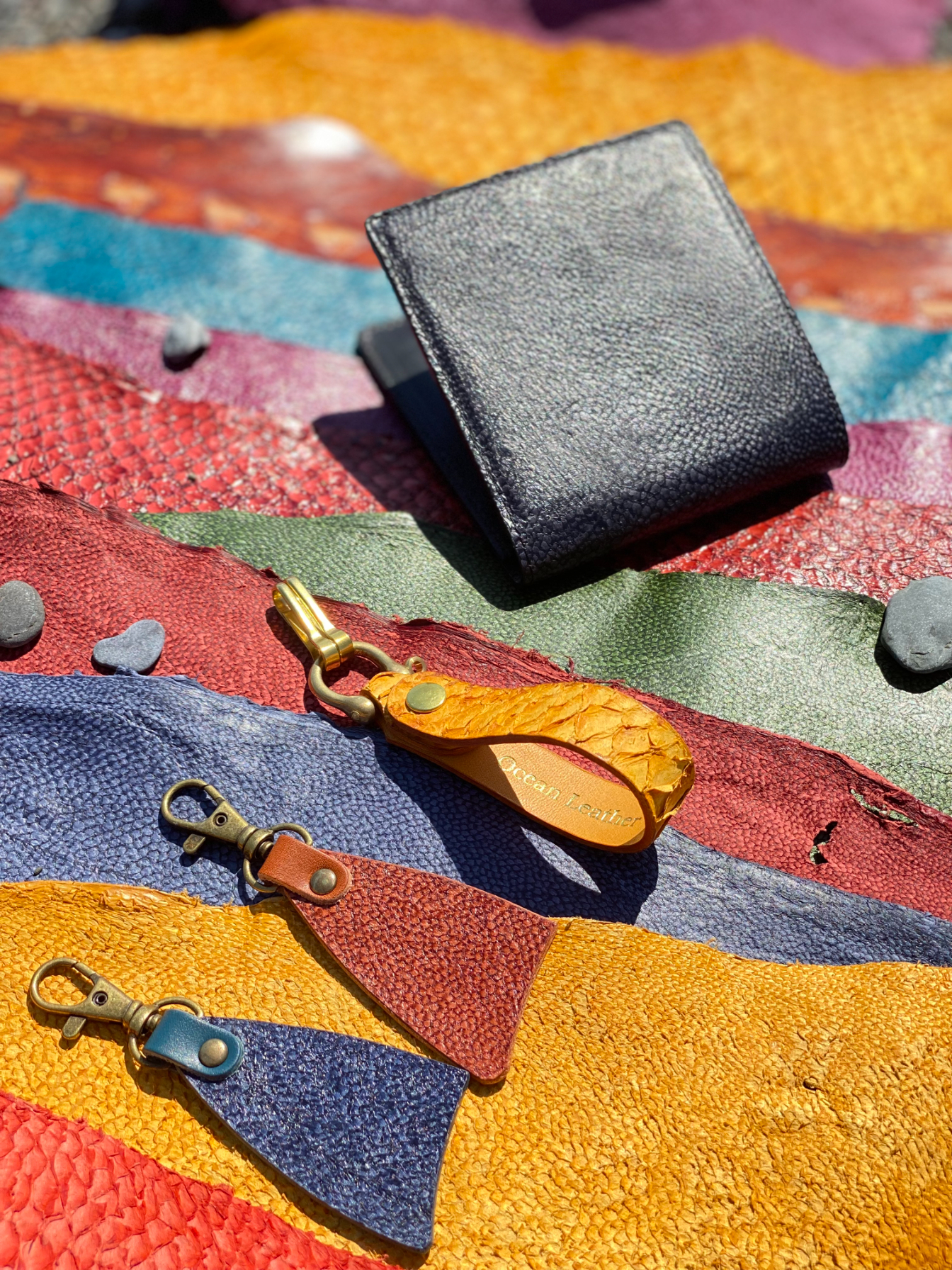
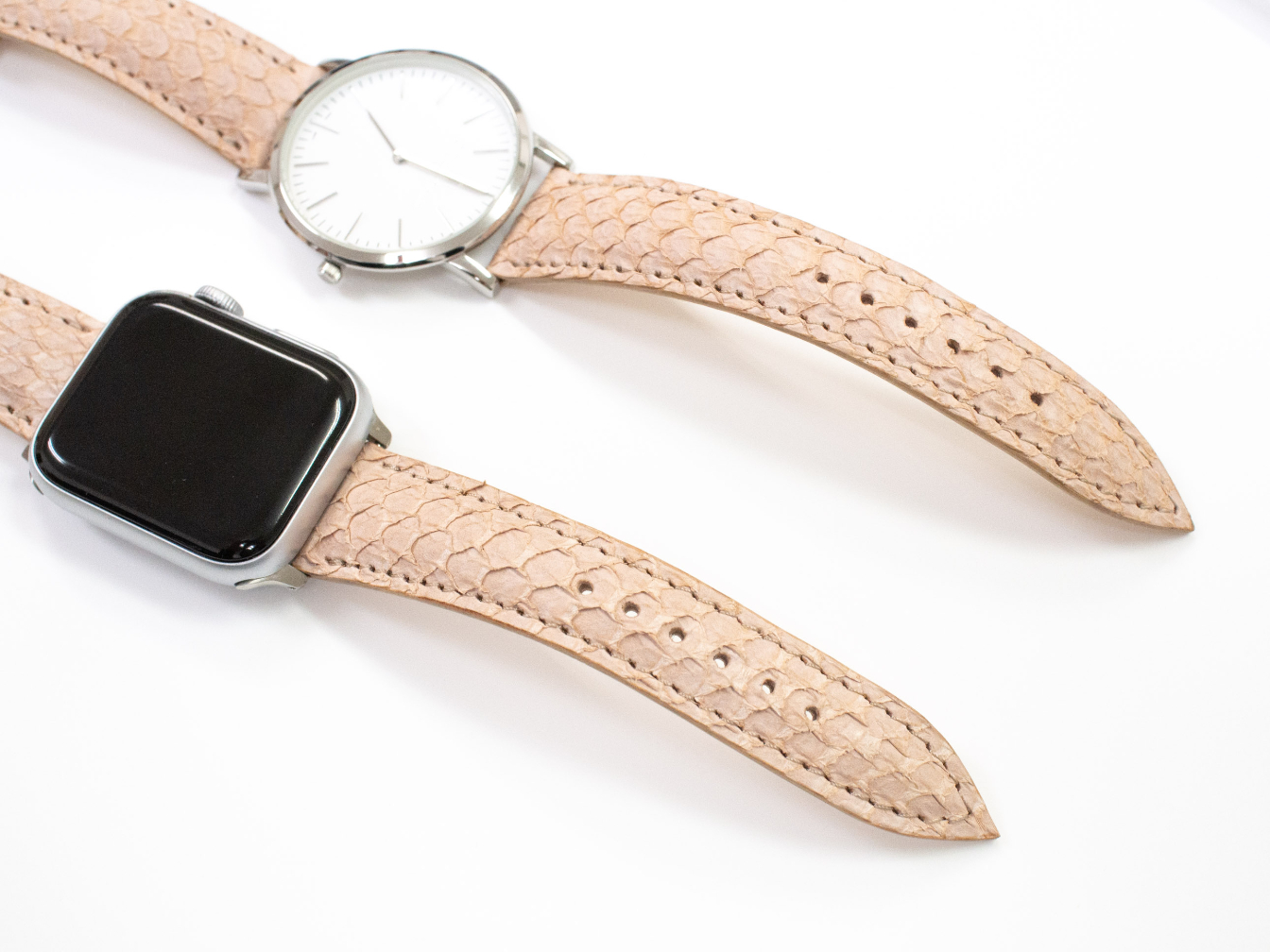

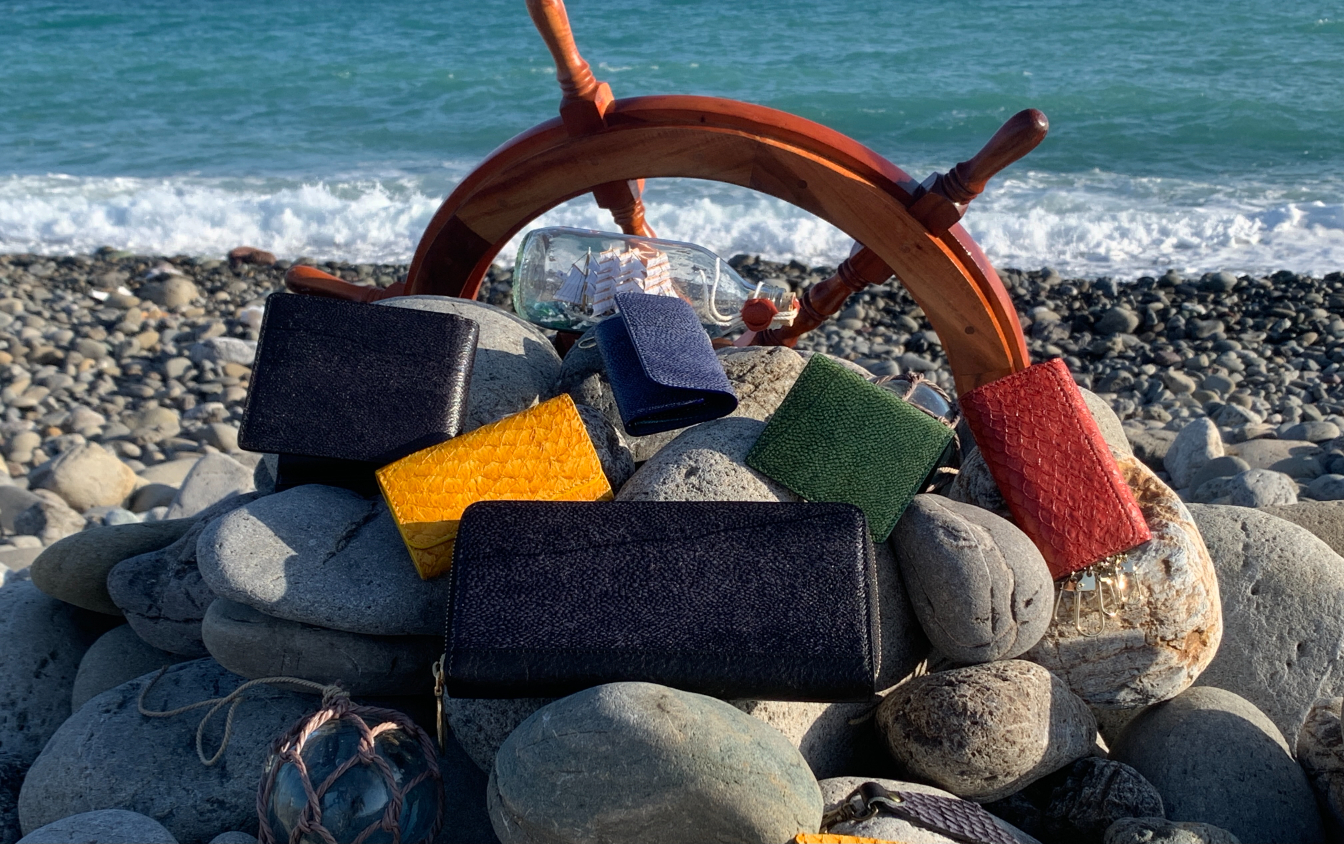
同社によると、生魚を刺身などに加工する際に出る魚の皮、頭、内臓などの廃棄部分は日本では年間66万トンもの量になる。魚屋などから仕入れた生皮をフィッシュレザーに仕上げるには、皮についた脂などの除去、塩漬け、なめし、染色、縫製などを経て、約1か月の時間がかかる。化学薬品を使わない自然由来の加工技術だ。
フィッシュレザーは、古来アイヌの人々が魚の皮を靴や服に加工していたという資料が残っているほど、日本では長い歴史がある素材。とはいえ、商業生産に乗せることは容易ではなかった。野口さんは、氷見市で魚の皮でサンダルを作るプロジェクトが始動したと聞きつけ、共同での研究をスタートしたものの、「最初は試行錯誤の連続。どうにか課題となっていた生臭さを解消し、革特有の柔らかさを実現するまで2年半を費やした」と振り返る。
「フィッシュレザーの商品を作るために魚を獲ることはしない。あくまで日頃私たちが食べるために調理され、廃棄されたものを使うことにこそ意義がある」と野口さんは語る。そして、自らの技術を広く共有して欲しいとの思いから、昨年、国連開発計画が南太平洋のサモアで計画している「魚の皮や廃棄物の有効活用法の開発」プロジェクトに参加企業として応募、今年5月からフィッシュレザーの技術指導を行うことになった。

この技術指導には、もうひとつのフィッシュレザー開発企業も加わる。2021年に高知県南国市でスタートしてブランド「「Ocean leather」(高橋大海代表)だ。同ブランドではブリやタイのほか、サケ、シイラ、チョウザメ、マグロなどのフィッシュレザーも製造。顧客企業のニーズに合わせたOEM生産(相手先ブランドによる生産)も請け負っている。
フィッシュレザーの普及に取り組む両社には、廃棄物に命を吹き込み蘇らせたいという共通の思いがある。そして、「魚の廃棄量を減らすことはもちろん、材料として買い取ることで水産業の振興にも貢献していきたい(高橋さん)」という社会貢献の意識も強い。
新しいチャレンジとなるサモアでの技術指導について、シンクシーの野口さんは「国によって生育する魚、食べる魚も違う。他国での支援を通して、フィッシュレザーの新たな可能性を探りたい」と語る。また、高橋さんも「今の技術を自分だけのものにするだけでなく、伝えていくことで一層の市場拡大を期待できる」と見ている。
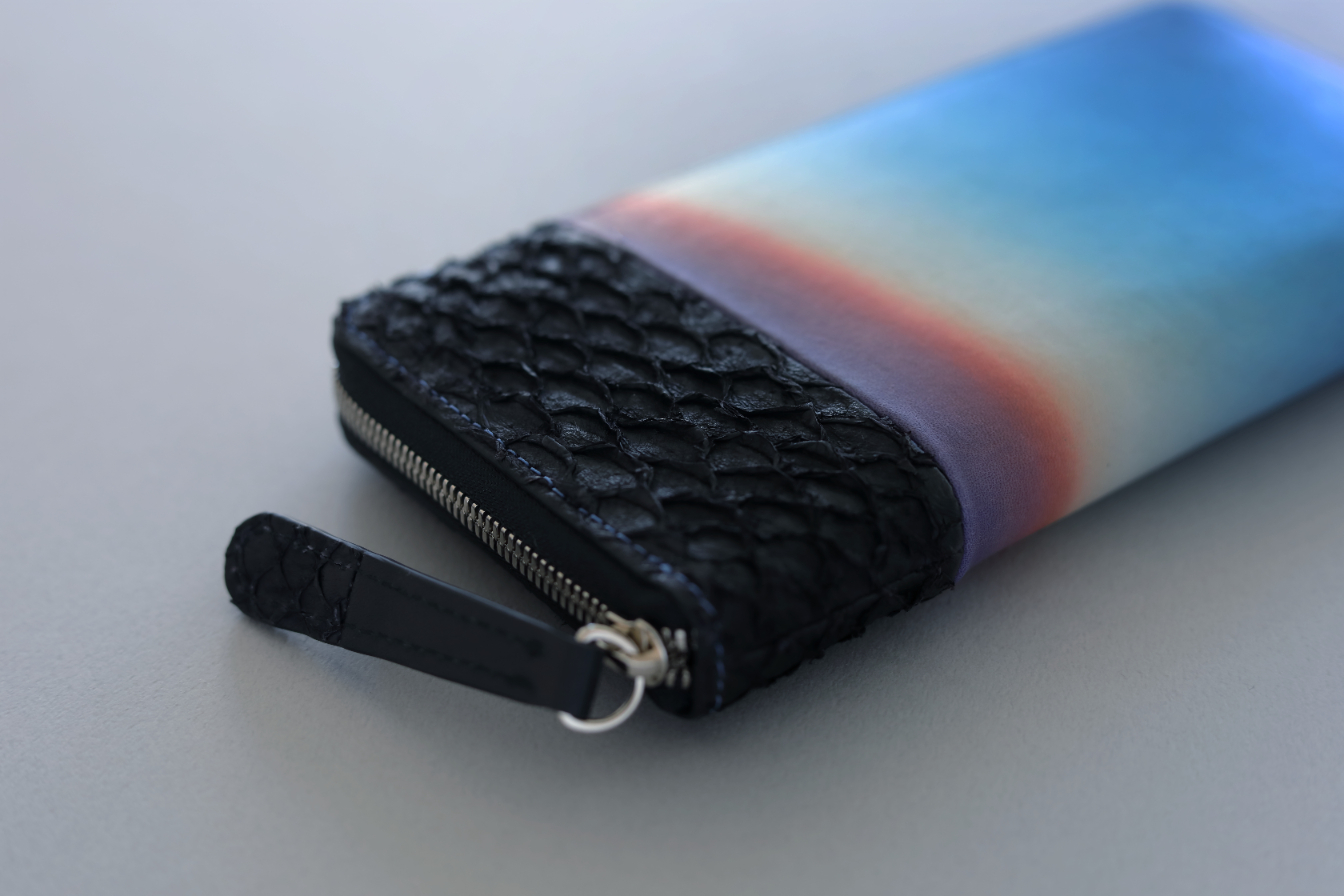
野口さんらの取り組みに共感し、フィッシュレザーの新ブランドを展開している企業もある。「フィッシュレザーの普及を後押ししたい」と語る岸原秀行さんは、今年に入り、レザーブランド「L‘ora blu」(株式会社GOODIE:大阪市北区)を立ち上げた。「フィッシュレザーを通して、多くの人が廃棄物や食肉文化の副産物である革製品について考えるきっかけになって欲しい」と岸原さんは話している。
記事:大平誉子 編集:北松克朗
トップ写真:Ocean Leather 提供
この記事に関するお問い合わせは、jstories@pacificbridge.jp にお寄せください。
***
***
本記事の英語版はこちらからご覧になれます。