J-STORIES ー 建設業の2代目社長だった鈴木正臣さんが「地震犠牲者ゼロ」をめざすビジネスに大きく舵を切ったのは、2016年8月24日にイタリア中部で起きた大規模地震の被害を現地で目の当たりにしたことがきっかけだった。マグニチュード6.2の激しい揺れで240人が死亡。がれきの中からまだ音を立てていたおもちゃを見つけた鈴木さんは、犠牲になった子供の痛々しい姿を思い浮かべ、胸が締め付けられた。
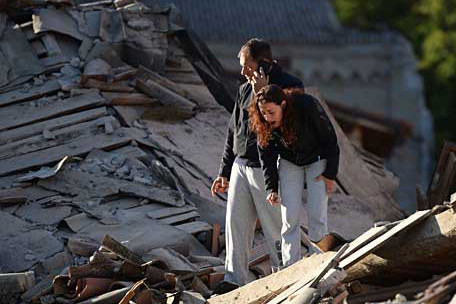
鈴木さんが取り組んでいるのは、東京大学と共同研究して生み出したペースト状の耐震材の普及だ。イタリアでは日本に比べ、レンガや石などを積み上げる組積造の建物が多く、その崩壊が甚大な被害を招く一因となった。
「家業を辞めてでも、自分の人生をかけ、全身全霊でこの耐震材の製造に取り組まなければならない」と鈴木さんは強く誓い、新会社Aster(東京都中央区)を創業、耐震材「Power Coating」の事業拡大に乗り出した。
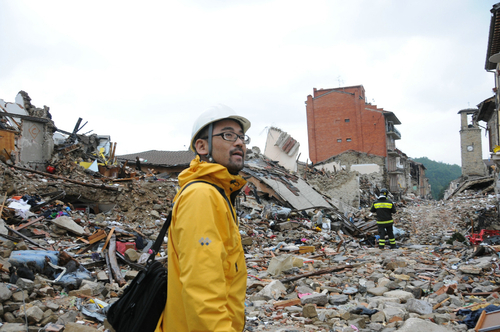
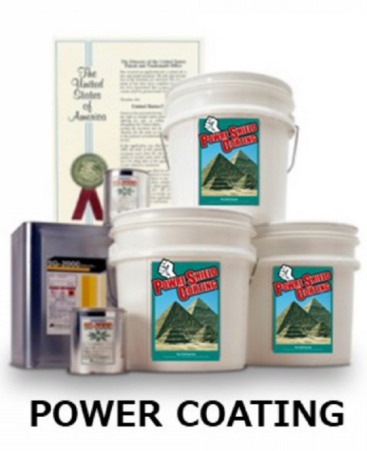
Power Coatingは、塗るだけで外壁にしなやかさを与え、耐震性を強化させることができる。一般的な高度樹脂の1/10〜1/20という価格設定で、特別な技術も不要なため誰でも使える手軽さがある。鈴木さんによると、築500年の既存の建物の耐震性も強化できるという。
レンガや石の建物は、高度な技術がいらず、原料の入手が安易で価格も安いことから、多くの国で現在も建設されているが、Asterによると震度3〜4で崩壊することもある。1915年ー2015年の100年間の地震による死者は、約80%が組積造式建物の崩壊の犠牲になったとの調査もある。世界では人口の約60%が住居している建物が地震に弱い造りをしていると言われる。
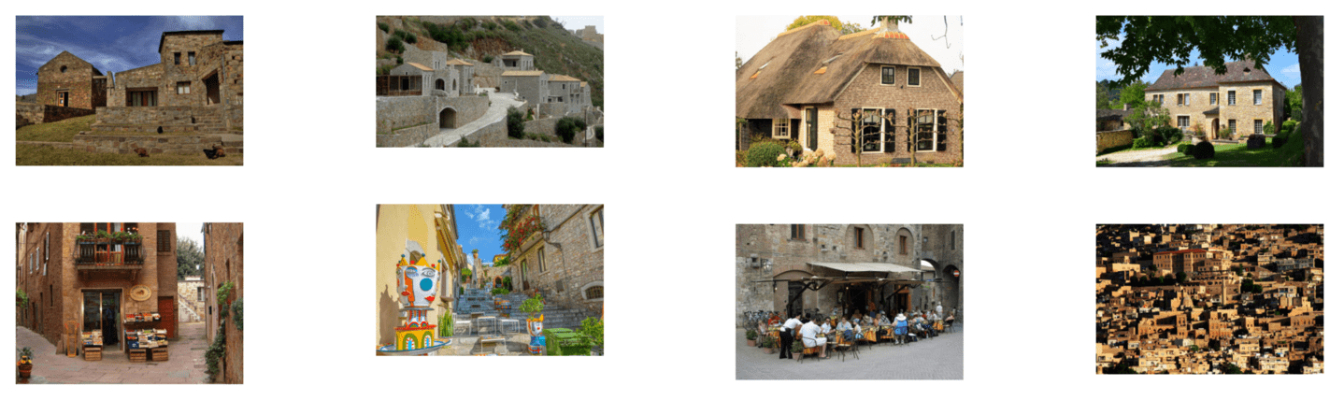
鈴木さんによると、同社の耐震材には世界各地から導入希望の声がかかっており、今後の大きな市場としては、フィリピン、ネパール、コロンビアを視野に入れている。また、主要な建築資材であるセメントは製造過程で排出される二酸化炭素(CO2)が問題となっており、Power Coatingがセメントの代替品にもなりうるのではないか、と鈴木さんは話す。成功すれば世界で毎年28億トン排出されている二酸化炭素の削減にも貢献できるとの期待がある。
一方、耐震建築の技術が進む日本では、これまで同社の技術が評価される機会が少なく、鈴木さんは幾度となく悔しい思いを経験したという。
同社は今年2月、日本経済新聞社が行ったベンチャー企業の事業モデルコンテストで、参加した105社の中からグランプリに選ばれた。
J-Storiesの取材に対し、鈴木さんは「社会の役に立つ製品を作ることとビジネスが両立できることを証明していきたいし、そういうものが今後は当たり前になるべきだと思う。この技術を成功させて、社会の役に立ってビジネスにもなる事業を行う人たちが続くといい」と語った。
- この記事は2022年5月に執筆されました。
記事:澤田祐衣 編集:北松克朗
トップ写真:stockcentral/Envato
この記事に関するお問い合わせは、 jstories@pacificbridge.jp にお寄せください。
***
***
本記事の英語版は、こちらからご覧になれます。